The powder metallurgy processing equipment employed is specifically designed to accurately simulate an industrial press-sinter-size sequence. Research is completed at all stages of the process including powder blending, compaction (uni-axial die and CIP), controlled atmosphere sintering, sizing/repressing, and secondary operations (heat treatment, shot peening, etc.).
Powder Compaction
Uni-axial Die Compaction of Powders
- Instron Model 200HVL
- Load Capacity = 1MN
- Maximum Pressure = 600MPa
- Self Contained Tool Sets Available for the Uni-Axial Die Compaction of:
- Discs (15mm, 30mm and 50mm OD)
- Transverse Rupture Strength Bars (12.7 x 31.7mm)
- Charpy Bars (12.7mm x 75mm)
- Rectangular Bars (20 x 90mm)
- Dog Bone Tensile Bars

Universal test frame and the self-contained tooling utilized to simulate industrial powder compaction operations.
Cold Isostatic Press (CIP)
- Avure Technologies
- Maximum Pressure = 415MPa
- Chamber Volume = 3500cm3
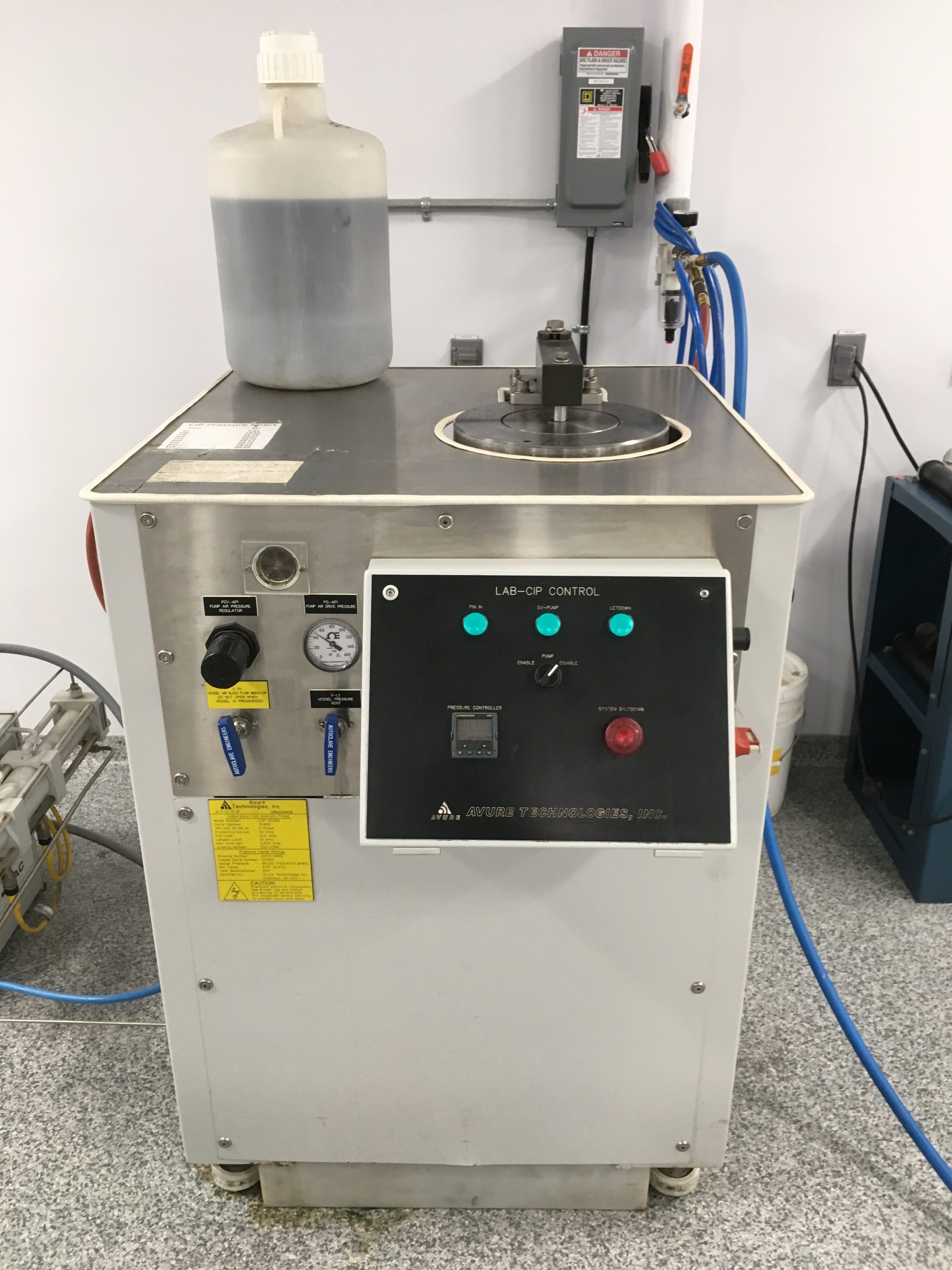
Avure Technolgies model LCIP 42260 cold isostatic press for compacting metal powders.
Controlled Atmosphere Sintering
Tube Furnace
- Lindberg Three-Zone Furnace
- Carbolite Three-Zone Furnace
- Stainless Steel Retort with Water Jacketed Cooling Section
- Atmospheres: Ar, N2, Mechanical Vacuum (10-2 Torr)
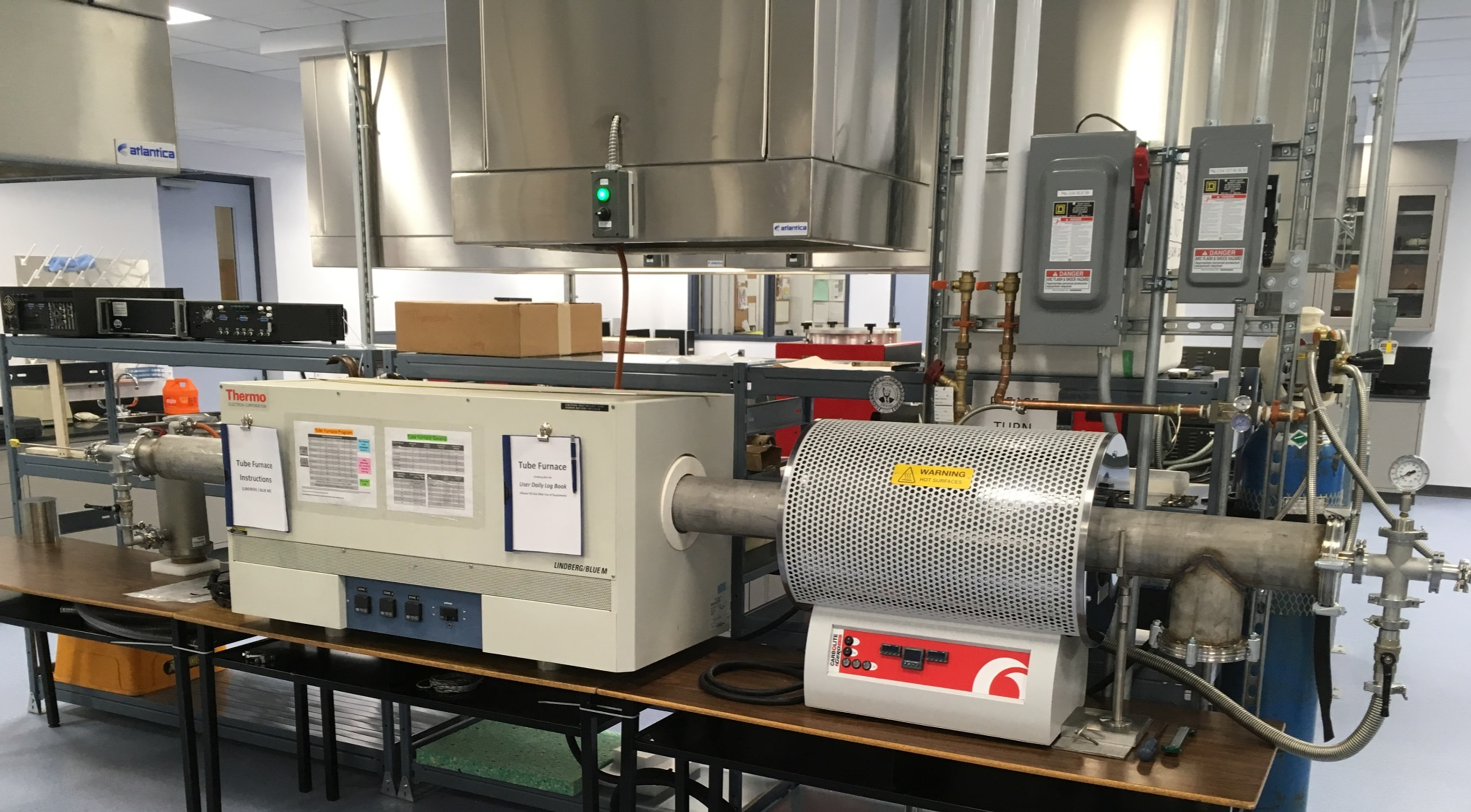
Customized tandem furnace assembly for sintering PM compacts under a controlled atmosphere.
Bell Jar Furnace
- Materials Research Furnaces
- Maximum Temperature = 1650°C
- Atmospheres: Ar, N2, H2, Mixed Gas, High Vacuum (10-5 Torr)
- Oxygen Monitor
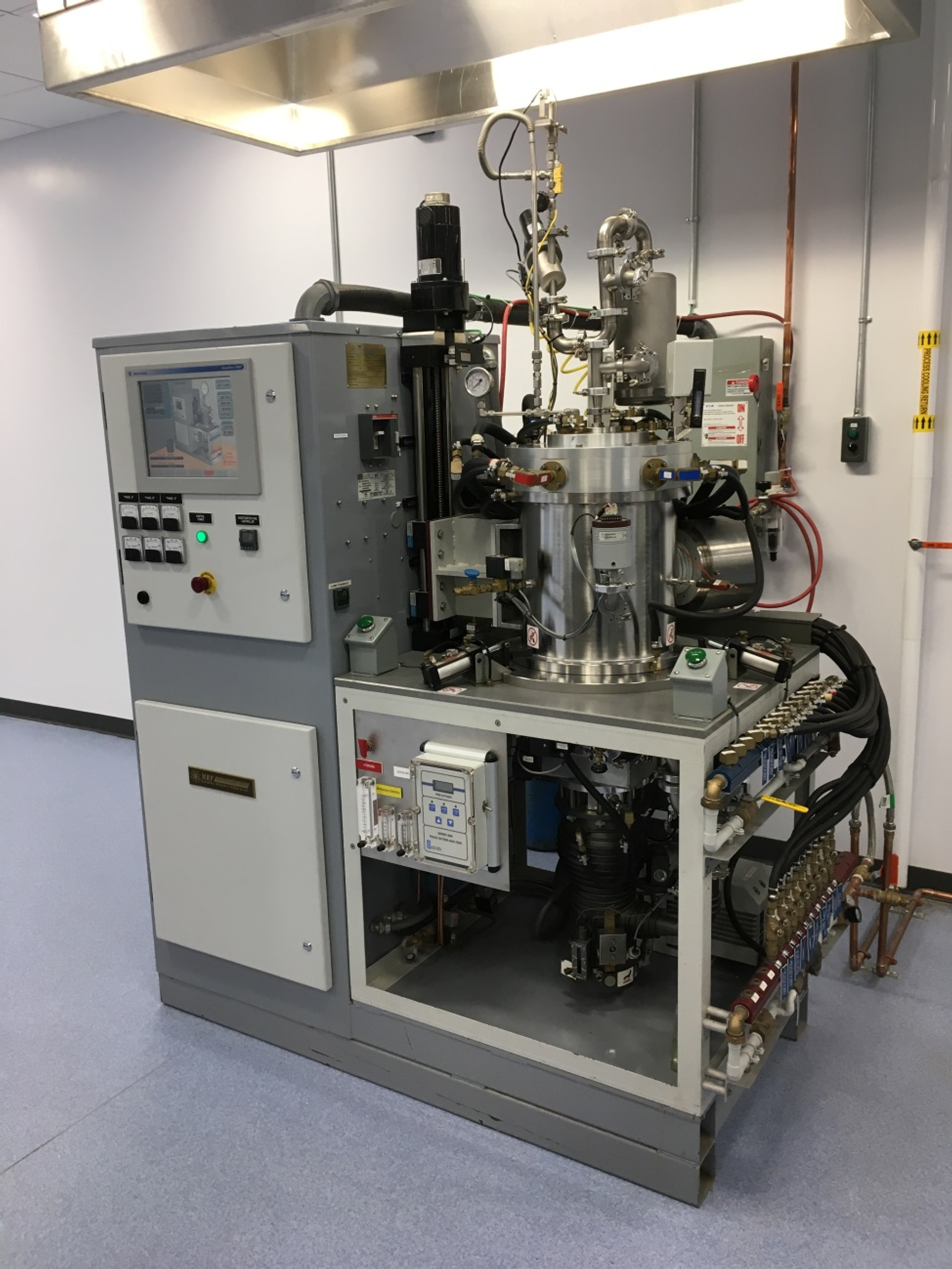
Multi-atmosphere bell jar furnace regularly utilized in sintering studies on a variety of different alloys (aluminum, nickel, iron, titanium, etc.).
Spark Plasma Sintering Furnace
- GT-Advanced Technologies
- Maximum Temperature = 2200°C
- Maximum Load = 100kN
- Atmospheres: Ar, N2, H2, Mixed Gas, Mechanical Vacuum (10-2 Torr)
- 20mm and 40mm OD graphite tooling
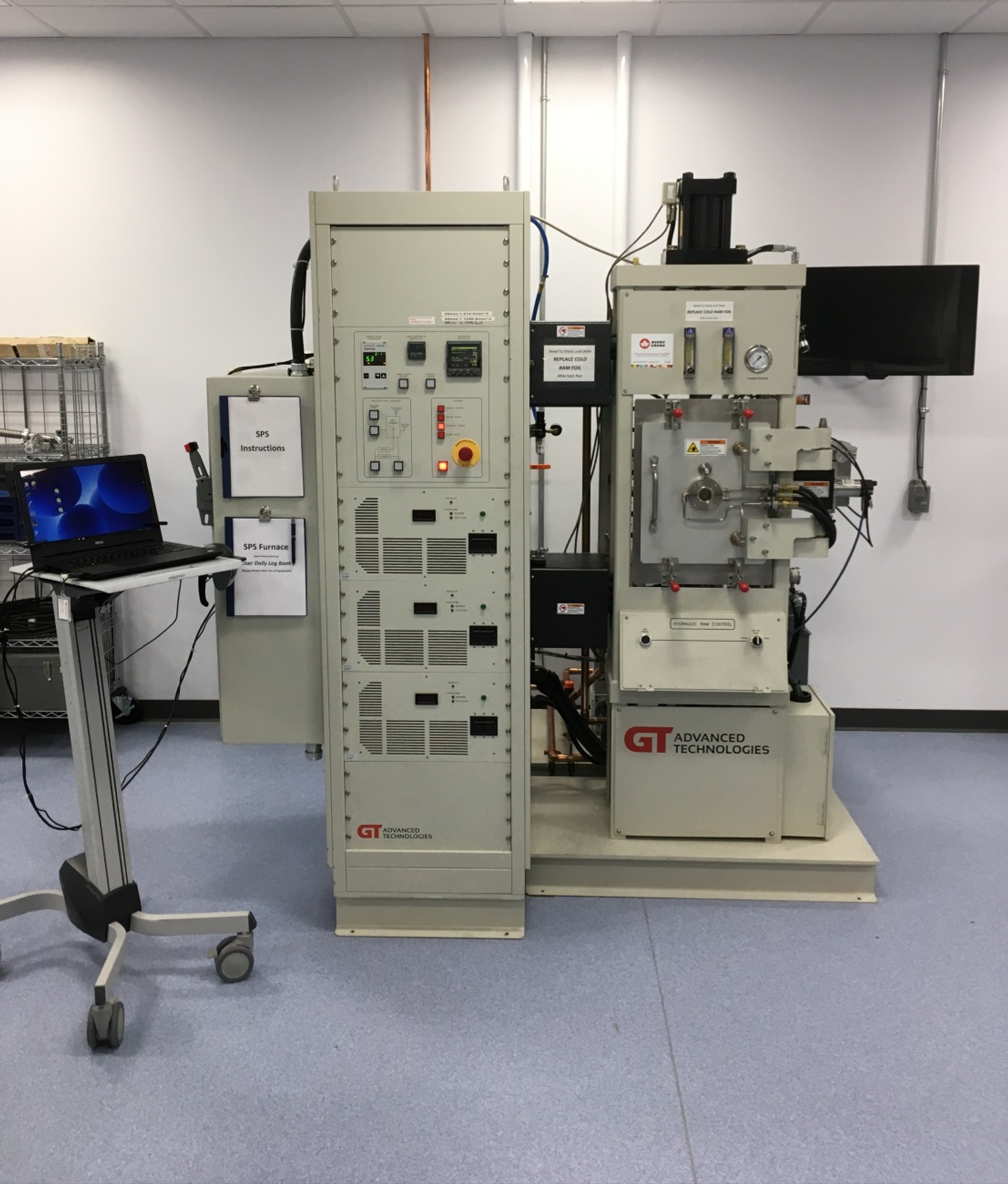
Spark plasma sintering furnace utilized to consolidate metallic, ceramic, and composite particulate materials.